Pozycja (xác định vị trí) jest uniwersalną (nhiều tác dụng; đa năng) tolerancją (kích cỡ, khối lượng, của một bộ phận có thể dao động mà không gây tác hại), która może być używana do kontroli położenia, współosiowości (đồng trục), orientacji lub przesunięcia osi elementu lub osi. Pozycja powinna być określona zawsze, gdy pozwalają na to wymagania projektowe. Kontrola ta daje możliwość wykorzystania (dùng, sử dụng; tận dụng) wielu zalet GD&T.
Pozycja to idealne położenie cechy wielkości w stosunku do układu lub układów odniesienia. Jest to pierwsza zasada. Powierzchnie nie mogą być kontrolowane za pomocą tolerancji położenia (powierzchnia może być kontrolowana za pomocą profilu tolerancji powierzchni). Tylko elementy o rozmiarze mogą mieć zastosowaną tolerancję położenia. Zobacz rysunek po prawej stronie.
Jak to działa? Tolerancja położenia definiuje jedno z poniższych:
- Strefa, w której środek, oś lub płaszczyzna środkowa elementu o rozmiarze może różnić się od prawdziwego (teoretycznie dokładnego) położenia.
- Tolerancja położenia może być określona w kontekście RFS, MMC lub LMC.
- Gdy jest określona na podstawie Regardless Feature of Size (RFS), kontrola TOP (tolerancja położenia) definiuje strefę tolerancji, w której musi znajdować się środek, oś lub płaszczyzna środkowa „Actual Mating Envelope (AME)” punktu sprzedaży.
- Gdy jest określona na podstawie MMC lub LMC, kontrola TOP definiuje granicę – często określaną jako warunek wirtualny – która nie może być naruszona przez powierzchnię lub powierzchnie rozpatrywanego elementu.
Jak ją zastosować? Tolerancja położenia jest określana za pomocą ramki kontrolnej elementu, w której wyświetlany jest symbol charakterystyczny „położenie”, a następnie przedział zawierający wartość tolerancji położenia. Wewnątrz przedziału, po wartości tolerancji położenia może następować symbol modyfikujący MMC lub LMC. Wszelkie dodatkowe modyfikatory, takie jak „tolerancja statystyczna” i/lub „przewidywana strefa tolerancji”, po których następuje jeden, dwa lub trzy oddzielne przedziały, z których każdy zawiera literę odniesienia do układu odniesienia. Po każdym odniesieniu do układu odniesienia może następować symbol modyfikujący MMC lub LMC, odpowiednio do typu cechy układu odniesienia i projektu.
Pozycja rzeczywista jest teoretycznie dokładnym położeniem cechy wielkości (FOS) określonej przez wymiary podstawowe. Wyrażone jako całkowite dopuszczalne odchylenie, jakie cecha może mieć od swojego „prawdziwego” położenia. W zależności od tego, jak jest określana, true position może oznaczać kilka różnych rzeczy. Może być używane z MMC (Max Material Condition), LMC (Least Material Condition), rzutowanymi tolerancjami (P) i płaszczyznami stycznymi (T).
Wymiary dla True Position: Dla każdego pojedynczego elementu kontrolowanego należy ustalić unikalne położenie rzeczywiste z podstawowymi wymiarami względem określonego DRF (Datum Reference Frame). Prawdziwe położenie jest nominalną lub idalną orientacją i lokalizacją elementu, a zatem środkiem wirtualnej granicy warunku lub strefy tolerancji położenia. Podstawowe wymiary mogą być przedstawione graficznie na rysunku lub wyrażone w formie tabeli na rysunku lub w dokumencie, do którego odnosi się rysunek.
- Wymiarowanie linii bazowej: Dla każdego z dwóch otworów Ø.376, wymiar bazowy pochodzi z każdej płaszczyzny DRF. Producenci preferują tę metodę, ponieważ bezpośrednio dostarcza im ona współrzędnych dla każdego prawdziwego położenia względem początku linii bazowej. Kontrola CMM jest uproszczona, używając jednego 0,0 początku dla obu otworów.
- Wymiarowanie łańcuchowe: Wymiar podstawowy 1.500 lokalizuje górny otwór Ø.500 bezpośrednio z płaszczyzny środkowej.
Jednak dolny otwór Ø.500 jest zlokalizowany z 2.500 wymiaru podstawowego od prawdziwej pozycji górnego otworu. Często mylimy 2.500 podstawowy jako pochodzący z rzeczywistej osi górnego otworu, a nie z jego prawdziwej pozycji. Producent potrzebujący współrzędnej dolnego otworu będzie musiał ją obliczyć 1.500 – 2.500 = – 1.000.
- Domniemane wymiarowanie symetrii: W wielu przypadkach obowiązujące wymiary podstawowe są implikowane przez widoki rysunków. Rzeczywiste pozycje dwóch otworów Ø.750 mają pojedynczy wymiar podstawowy 3.000 pomiędzy nimi, ale nie ma wymiaru, który odnosiłby którykolwiek z otworów do płaszczyzn DRF. Ponieważ otwory wydają się symetryczne względem płaszczyzny środkowej DRF, ta symetryczna relacja podstawowa jest implikowana (ngụ ý, bao hàm, ám chỉ).
- Implikowane zerowe wymiary podstawowe: Widok implikuje relację otworu Ø.750 do płaszczyzn DRF reprezentowanych przez linie środkowe widoku. Oczywistym jest, że podstawowa orientacja otworu wynosi 0°, a jego podstawowe odsunięcie od środka wynosi 0. Te implikowane zerowe wartości podstawowe nie muszą być wyjaśniane (giải nghĩa, giải thích).
- Implikowane podstawowe kąty 90°: Kąt podstawowy 90° ma zastosowanie, gdy linie środkowe cech we wzorze (lub powierzchnie pokazane pod kątem prostym na rysunku) są zlokalizowane i zdefiniowane przez wymiary podstawowe i nie jest określony żaden kąt.
- Wymiarowanie za pomocą współrzędnych biegunowych: Zamiast przez współrzędne prostokątne odpowiadające (tương đương hoặc tương tự) dwóm prostopadłym osiom DRF, rzeczywiste położenie ośmiu otworów Ø.750 jest zdefiniowane przez współrzędne biegunowe dla kąta i średnicy. Ø6.000 „okrąg śruby” jest w zasadzie wyśrodkowany na przecięciu płaszczyzn odniesienia, a dwa kąty podstawowe 45°
pochodzą z płaszczyzny DRF. Rysunki b i c pokazują alternatywne podejścia, które dają równoważne wyniki, oparte na różnych metodach i podstawowych zasadach. Wszystkie przedstawione metody są dopuszczalne. Projektant może wybrać pomiędzy wymiarowaniem linii bazowej i wymiarowaniem łańcuchowym. Chociaż obie metody dają identyczne wyniki, preferowane jest wymiarowanie w linii bazowej, nawet jeśli projektant musi wykonać pewne obliczenia, aby wyrazić wszystkie wymiary pochodzące od początku układu odniesienia. Wykonanie tego raz wykluczy (ngăn ngừa, làm cho không thể xảy ra) niezliczone, podatne na błędy obliczenia w przyszłości.
Datumy dla kontroli pozycji: Każda tolerancja pozycyjna powinna odnosić się do jednej, dwóch lub trzech cech układu odniesienia. DRF nie musi ograniczać wszystkich sześciu stopni swobody, tylko te, które są niezbędne do ustanowienia unikalnej orientacji i lokalizacji dla prawdziwej pozycji. Przykład: DRF określona na prawym rysunku ogranicza tylko cztery stopnie swobody. Pozostałe dwa stopnie, obrót wokół i przemieszczenie wzdłuż osi układu odniesienia, nie mają wpływu na rzeczywiste położenie kontrolowanego elementu. W związku z tym dalsze odniesienia do układu odniesienia są bezsensowne i mylące.
Dla wielu tolerancji położenia, takich jak te na prawym rysunku, widok rysunku sprawia, że jest całkiem oczywiste, które cechy części są pochodzenia, nawet jeśli nie zostały one zidentyfikowane jako cechy układu odniesienia i odniesione w ramce kontrolnej elementu. Chociaż możemy się zgodzić, że lewa i dolna krawędź części są wyraźnie cechami układu odniesienia, możemy się nie zgodzić co do ich pierwszeństwa w ustalaniu orientacji DRF. W innym przykładzie, gdy część ma wiele współosiowych średnic, może być oczywiste dla projektanta, ale bardzo niejasne dla czytelnika, która średnica ma być cechą układu odniesienia. Z tego powodu, Y14.5 nie zezwala już na domniemane układy odniesienia.
Tolerancja położenia jest geometrycznym wymiarowaniem i tolerowaniem (GD&T) kontroli lokalizacji używanym na rysunkach inżynierskich w celu określenia pożądanej lokalizacji, jak również dopuszczalnych odchyleń od położenia elementu na części.
- Tolerancja położenia określa dopuszczalne odchylenie od prawdziwego położenia.
- Tolerancja dla prawdziwego położenia lub wymiaru podstawowego musi pochodzić z tolerancji geometrycznej.
- Przy stosowaniu tolerancji położenia należy określić prawdziwe położenie elementu wielkości.
Wymagania dotyczące tolerancji położenia:
- Musi być stosowana do elementu o rozmiarze lub układu elementów o rozmiarze.
- Wymiary podstawowe stosowane do określenia prawdziwego położenia.
- Muszą być stosowane odniesienia do datum (z wyjątkiem stosowania do średnic współosiowych).
- RFS jest stanem domyślnym, chyba że określono MMC lub LMC.
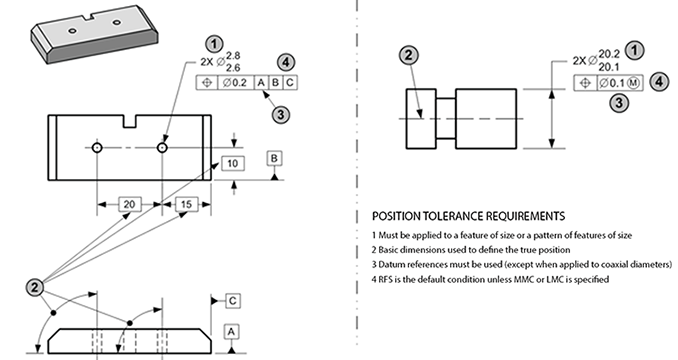
Dwa powszechnie stosowane kształty stref dla tolerancji położenia.
Modyfikatory, które mogą być stosowane z tolerancją położenia oraz kiedy każdy modyfikator stanu materiału (MMC, LMC lub RFS) powinien być stosowany w tolerancji położenia. Modyfikator M obniża koszt produkcji. Modyfikator P jest używany do wyrównania.
Dwie interpretacje stref tolerancji dla tolerancji położenia. Pozycjonowanie osi RFS i pozycjonowanie powierzchni MMC.
- Kiedy należy stosować interpretację powierzchniową dla tolerancji geometrycznej? Gdy modyfikator MMC jest określony w ramce kontrolnej elementu. Interpretacja powierzchniowa dla tolerancji położenia na wzorcu otworów. Interpretacja powierzchniowa dla tolerancji położenia na szerokości.
Interpretacja osi/płaszczyzny środkowej dla tolerancji położenia na wzorze otworów: Oś niepowiązanej rzeczywistej obwiedni współpracującej musi znajdować się w strefie tolerancji. Cylindry strefy tolerancji są zlokalizowane i zorientowane według wymiarów podstawowych. Zmienność orientacji osi jest ograniczona przez cylinder strefy tolerancji. Wzór otworów kontrolowany za pomocą TOP przy użyciu RFS. Średnice współosiowe kontrolowane przy użyciu TOP z wykorzystaniem RFS.
Interpretacja płaszczyzny środkowej dla tolerancji położenia na szerokości A: Płaszczyzna środkowa niepowiązanej, rzeczywistej, współpracującej obwiedni musi znajdować się w strefie tolerancji. Symulator płaszczyzny odniesienia składa się z dwóch równoległych płaszczyzn stykających się z częścią w celu ustalenia płaszczyzny środkowej płaszczyzny odniesienia.
Tolerancja położenia i warunki, które stosuje się w RFS:
- Gdy tolerancja położenia jest stosowana w RFS, tolerancja premii jest niedozwolona.
- Gdy tolerancja położenia jest stosowana w RFS, stosowana jest interpretacja osi/płaszczyzny środkowej.
- Gdy tolerancja położenia jest stosowana w RFS, strefa tolerancji jest zlokalizowana przez wymiary podstawowe.
Tolerancja położenia i warunki, które mają zastosowanie w MMC:
- Gdy tolerancja położenia jest stosowana w MMC, dozwolona jest tolerancja dodatkowa.
- Gdy tolerancja położenia jest stosowana w MMC, interpretacja oś/płaszczyzna środkowa nie jest stosowana.
- Gdy tolerancja położenia jest stosowana w MMC, strefa tolerancji jest zlokalizowana przez wymiary podstawowe.
Tolerancja położenia i cechy kątowe: Tolerancja pozycyjna jest szczególnie odpowiednia dla cech kątowych na całej długości. Zakłada to (cho là, coi như là), że cecha nie ma funkcjonalnego interfejsu (mặt phân giới) poza swoją własną długością i szerokością (bề ngang, bề rộng, khổ). Jednak na prawym rysunku, sworzeń jest wciśnięty w kontrolowany otwór i oczekuje się, że będzie pasował do innego otworu w pokrywie. Elementem współpracującym nie jest sam otwór na kołek, ale raczej kołek, który reprezentuje rzut otworu. Podobnie, interfejs współpracujący nie znajduje się na długości otworu na sworzeń, ale powyżej otworu, w grubości płyty pokrywy. Patrz rysunek. Ustalanie prawdziwych pozycji na podstawie domniemanego układu odniesienia – częsty błąd.
Gdyby otwór na sworzeń był idealnie prostopadły do płaszczyzny styku dwóch części, nie byłoby różnicy między położeniem otworu i sworznia. Każde odchylenie (hình có góc) wprowadza jednak rozbieżność (sự khác nhau) w położeniu. Ta rozbieżność jest proporcjonalna (tương ứng về cỡ, số lượng hoặc mức độ ; có tỷ lệ đúng; cân xứng) do długości projekcji. Zatem (do đó, theo đó, vì thế, vì vậy), bezpośrednie kontrolowanie położenia samego otworu na kołek jest nieadekwatne (không tương xứng, không xứng, không thích đáng, không thoả đáng) do zapewnienia montowalności. W związku z tym (bởi vậy, cho nên, vì thế, vậy thì), należało kontrolować położenie rzutu otworu (hình chiếu), o którym można myśleć jak o fantomowym kołku. osiąga się to za pomocą tolerancji pozycyjnej zmodyfikowanej o strefę tolerancji rzutowanej.
Tolerancja pozycyjna i strefa tolerancji rzutowanej. Zastosowanie tej koncepcji jest zalecane w przypadku, gdy zmiana prostopadłości otworów gwintowanych lub wciskanych może spowodować, że elementy złączne, takie jak śruby, śruby dwustronne lub sworznie, będą kolidować ze współpracującymi częściami. Na rysunku 1.a, interferencja może wystąpić, gdy tolerancja jest określona dla położenia gwintowanego lub wciskanego otworu, a otwór jest nachylony w granicach położenia. W przeciwieństwie do zastosowania łącznika pływającego, w którym występują tylko otwory luźne, położenie łącznika stałego jest regulowane przez pochylenie produkowanego otworu, w którym jest on montowany. Rysunek 1.b ilustruje, jak koncepcja projektowanej strefy tolerancji realistycznie traktuje stan przedstawiony na poprzednim rysunku 1.a. Należy zauważyć, że istotna jest zmiana prostopadłości części śruby przechodzącej przez część współpracującą. Położenie i prostopadłość gwintowanego otworu są ważne tylko w takim stopniu, w jakim wpływają na przedłużoną część łącznika. Gdy względy konstrukcyjne wymagają ściślejszej kontroli prostopadłości otworu gwintowanego niż ta dozwolona przez tolerancję położenia, można określić tolerancję orientacji stosowaną jako przewidywaną strefę tolerancji.
Przewidywana strefa tolerancji jest definiowana w celu przewidywania ostatecznych wymiarów i lokalizacji cech na komponencie lub zespole podlegającym spiętrzeniu tolerancji. Projektowana strefa tolerancji wychodzi poza zakres tolerancji elementu o danym rozmiarze. Projektowana strefa tolerancji jest określana przez umieszczenie symbolu P z okręgiem za wartością tolerancji w ramce kontrolnej elementu pozycyjnego. Ustanawia to stałą rozmiarowo (kích thước, cỡ, khổ không thay đổi) centralną strefę tolerancji ograniczoną albo dwiema równoległymi płaszczyznami oddzielonymi od siebie odległością równą określonej tolerancji, albo cylindrem o średnicy równej określonej tolerancji. Dla otworów nieprzelotowych i innych zastosowań, gdzie kierunek rzutowania jest oczywisty, długość rzutowania może być określona za symbolem w ramce kontrolnej elementu. Oznacza to, że rzutowana strefa tolerancji kończy się na powierzchni czołowej części i w określonej odległości od powierzchni czołowej części (z dala od części i równolegle do osi położenia rzeczywistego lub płaszczyzny środkowej). Długość rzutu powinna być równa maksymalnemu wydłużeniu współpracującego interfejsu. Na rysunku a (przykład sworznia i nakładki). długość występu musi być równa maksymalnej grubości nakładki .38. W razie potrzeby zakres i kierunek projektowanej strefy tolerancji są pokazane na widoku rysunku jako zwymiarowana wartość z ciężką linią łańcuchową narysowaną obok linii środkowej elementu, jak na rysunku. b.
- Na RFS: Przedłużona oś lub płaszczyzna środkowa rzeczywistej obwiedni elementu (jak zdefiniowano w Elementy pochodne) musi być zawarta w projektowanej strefie tolerancji.
- Na MMC: Przedłużona oś lub płaszczyzna środkowa obowiązującej granicy doskonałej formy MMC poziomu 2 (jak zdefiniowano w Poziom 2 – Ogólna forma elementu) musi być zawarta w projektowanej strefie tolerancji. W tym przykładzie wyjaśniono, że w miarę jak rozmiar elementu odbiega od MMC, element bardziej luźno dopasowuje się do granicy idealnej formy MMC. Pozwala to na większe odchylenia w orientacji i/lub lokalizacji elementu. Odejście otworu od MMC pozwala na montaż z pasującym sworzniem, którego oś znajduje się w dowolnym miejscu strefy stożkowej (hình nón). Alternatywna metoda środka opisana w (Poziom 2 – Ogólna forma elementu) nie może być stosowana dla projektowanej strefy tolerancji. Jej tolerancja bonusowa po prostu powiększyłaby projektowaną strefę tolerancji równomiernie na całej jej długości, nie naśladując prawdziwego potencjału funkcjonalnego elementu.
- W LMC: (strona 5-120)…
Weryfikuj tolerancję położenia za pomocą modyfikatora projektowanej strefy tolerancji: Jedną z powszechnych metod weryfikacji projektowanej strefy tolerancji jest użycie kołka pomiarowego włożonego do elementu tolerancji o rozmiarze z przedłużeniem wystającym na wysokość projektowanej strefy tolerancji. Wysokość projektowanej strefy tolerancji jest często określana przez maksymalną wysokość otworu w części współpracującej.
Tolerancja pozycyjna w MMC: Tolerancja pozycyjna stosowana w MMC może być wyjaśniona w kategoriach powierzchni lub osi elementu wielkości. W niektórych przypadkach ekstremalnej odchyłki kształtu (w granicach wielkości) lub odchyłki orientacji otworu, tolerancja w zakresie osi może nie być dokładnie równoważna tolerancji w zakresie powierzchni. Patrz Im_1-13. W takich przypadkach interpretacja powierzchni ma pierwszeństwo. W niektórych przypadkach, dodatkowa tolerancja może pośrednio przynieść korzyści cechom innym niż ta, która odeszła od MMC.
- Interpretacja powierzchniowa: Przy zachowaniu określonych granic wielkości cechy, żaden element powierzchni nie może naruszać teoretycznej granicy (warunku wirtualnego) znajdującej się w prawdziwym położeniu. Patrz Im_1-14.
- Kiedy należy stosować interpretację powierzchniową dla tolerancji geometrycznej? Gdy modyfikator MMC jest określony w ramce kontrolnej elementu, zobacz (Interpretacja powierzchniowa dla położenia na wzorze otworów – Interpretacja powierzchniowa dla tolerancji położenia na szerokości – Interpretacja osiowa/płaszczyznowa dla tolerancji położenia na wzorze otworów – Interpretacja płaszczyzny środkowej dla tolerancji położenia na szerokości).
- Interpretacja osiowa lub płaszczyzny środkowej: Gdy cecha o wielkości jest w MMC, jej oś lub płaszczyzna środkowa musi mieścić się w strefie tolerancji zlokalizowanej w prawdziwym położeniu. Wielkość tej strefy jest równa tolerancji położenia. Patrz Im_1-15, (notatka/ilustracje nr, 1 i 2). Ta strefa tolerancji określa również granice zmienności orientacji osi lub płaszczyzny środkowej elementu o danej wielkości w stosunku do powierzchni odniesienia. Zob. Im_1-15, (uwaga/ilustracja nr 3). Określona strefa tolerancji ma zastosowanie tylko wtedy, gdy cecha wymiarowa znajduje się w MMC. Gdy niepowiązany rzeczywisty rozmiar obwiedni elementu o rozmiarze różni się od MMC, powstaje dodatkowa tolerancja położenia. Patrz Im_1-16. Ten wzrost tolerancji położenia jest równy różnicy między określoną maksymalną granicą stanu materiału wielkości (MMC) a niepowiązaną rzeczywistą wielkością powłoki współpracującej. Gdy niepowiązany rzeczywisty rozmiar powłoki współpracującej odbiegał od MMC, określona tolerancja położenia dla cechy o rozmiarze może być większa niż podana wartość i nadal spełniać wymagania funkcjonalności i zamienności.
Określanie tolerancji położenia w MMC: Gdy symbol maksymalnego warunku materiałowego (MMC) jest określony w celu modyfikacji tolerancji cechy o rozmiarze w ramce kontrolnej cechy, stosuje się następujące dwa wymagania:
- Określona tolerancja ma zastosowanie przy rozmiarze MMC cechy. MMC elementu o rozmiarze to największy wałek i najmniejszy otwór. Rozmiar MMC elementu nie powinien być mylony z modyfikatorem MMC, kółkiem M.
- Jak rzeczywisty rozmiar obwiedni elementu odbiega od MMC w kierunku LMC, tolerancja dodatkowa jest osiągana w dokładnej wielkości tego odejścia.
.