La posizione (xác định vị trí) è una tolleranza versatile (nhiều tác dụng; đa năng) (kích cỡ, khối lượng, của một bộ phận có thể dao động mà không gây tác hại) che può essere usata per controllare posizione, coassialità (đồng trục), orientamento o offset di un elemento o asse del pezzo. La posizione dovrebbe essere specificata ogni volta che i requisiti di progettazione lo permettono. Questo controllo fornisce l’opportunità di utilizzare (dùng, sử dụng; tận dụng) molti dei vantaggi del GD&T.
La posizione è la posizione perfetta di una caratteristica di dimensione in relazione a uno o più datum. Questa è la prima regola. Le superfici non possono essere controllate con una tolleranza di posizione (la superficie può essere controllata con un profilo di una tolleranza di superficie). Solo le caratteristiche di dimensione possono avere una tolleranza di posizione applicata a loro. Vedi la figura a destra.
Come funziona? Una tolleranza di posizione definisce una delle seguenti cose:
- Una zona entro la quale il centro, l’asse o il piano centrale di una caratteristica di dimensione può variare da una posizione vera (teoricamente esatta).
- Una tolleranza di posizione può essere specificata in un contesto RFS, MMC, o LMC.
- Quando è specificato su una base RFS (Regardless Feature of Size), un controllo TOP (tolleranza di posizione) definisce una zona di tolleranza che il centro, l’asse o il piano centrale del “Actual Mating Envelope (AME)” di una POS deve essere entro.
- Quando specificato su una base MMC o LMC, un controllo TOP definisce un confine – spesso indicato come la condizione virtuale – che non può essere violato dalla superficie o dalle superfici della caratteristica considerata.
Come applicarla? Una tolleranza posizionale è specificata usando un riquadro di controllo della caratteristica che mostra il simbolo della caratteristica “posizione” seguito da uno scomparto contenente il valore della tolleranza posizionale. All’interno dello scomparto, il valore di tolleranza posizionale può essere seguito da un simbolo di modifica MMC o LMC. Qualsiasi modificatore aggiuntivo, come “tolleranza statistica” e/o “zona di tolleranza proiettata” seguita da uno, due o tre scomparti separati, ciascuno contenente una lettera di riferimento dell’origine. Ogni riferimento all’origine può essere seguito da un simbolo di modifica MMC o LMC, a seconda del tipo di caratteristica dell’origine e del progetto.
La vera posizione è la posizione teoricamente esatta di una caratteristica di dimensione (FOS) definita dalle dimensioni di base. Espressa come la variazione totale ammissibile che una caratteristica può avere dalla sua posizione “vera”. A seconda di come viene definito, true position può significare diverse cose. Può essere usata con MMC (Max Material Condition), LMC (Least Material Condition), tolleranze proiettate (P), e piani tangenti (T).
Dimensioni per True Position: Per ogni singolo elemento controllato, deve essere stabilita una posizione vera unica con dimensioni di base relative ad un DRF (Datum Reference Frame) specificato. La posizione reale è l’orientamento e la posizione nominale o idale dell’elemento e quindi il centro del confine della condizione virtuale o della zona di tolleranza posizionale. Le dimensioni di base possono essere mostrate graficamente sul disegno, o espresse in forma di tabella sul disegno o in un documento a cui fa riferimento il disegno.
- Dimensionamento della linea di base: Per ciascuno dei due fori Ø.376, una quota di base ha origine da ogni piano del DRF. I fabbricanti preferiscono questo metodo perché fornisce loro direttamente le coordinate per ogni posizione vera rispetto all’origine del dato. L’ispezione della CMM è semplificata, utilizzando una singola origine 0,0 per entrambi i fori.
- Quotatura a catena: Una quota base di 1.500 localizza il foro superiore di Ø.500 direttamente dal piano centrale.
Tuttavia, il foro inferiore di Ø.500 si trova con una quota base di 2.500 dalla posizione reale del foro superiore. Spesso confondiamo la base 2.500 come proveniente dall’asse reale del foro superiore, piuttosto che dalla sua vera posizione. Un fabbricante che ha bisogno della coordinata del foro inferiore dovrà calcolarla 1,500 – 2,500 = – 1,000.
- Dimensionamento della simmetria implicita: In molti casi, le dimensioni di base applicabili sono iplicate dalle viste del disegno. Le posizioni reali dei due fori Ø.750 hanno una sola quota base di 3.000 tra di loro, ma nessuna quota che metta in relazione uno dei due fori con i piani del DRF. Poiché i fori appaiono simmetrici rispetto al piano centrale del DRF, quella relazione di base simmetrica è implicita (ngụ ý, bao hàm, ám chỉ).
- Dimensioni di base zero implicite: La vista implica la relazione del foro Ø.750 con i piani del DRF come rappresentato dalle linee centrali della vista. Ovviamente, l’orientamento di base del foro è 0° e il suo offset di base dal centro è 0. Questi valori zero-base impliciti non hanno bisogno di essere spiegati (giải nghĩa, giải thích).
- Angoli di base impliciti di 90°: Un angolo di base di 90° si applica quando le linee centrali delle caratteristiche in un modello (o le superfici mostrate ad angolo retto su un disegno) sono situate e definite dalle dimensioni di base e nessun angolo è specificato.
- Dimensionamento delle coordinate polari: Piuttosto che da coordinate rettangolari corrispondenti (tương đương hoặc tương tự) a due assi perpendicolari del DRF, la posizione reale degli otto fori Ø.750 è definita da coordinate polari per angolo e diametro. Il “cerchio dei bulloni” Ø6.000 è sostanzialmente centrato sull’intersezione dei piani di riferimento, e i due angoli di base di 45°
hanno origine da un piano del DRF. Le figure b e c mostrano approcci alternativi che danno risultati equivalenti, basati su vari metodi e regole fondamentali. Tutti i metodi presentati sono accettabili. Il progettista può scegliere tra la linea di base e il dimensionamento a catena. Mentre entrambi i metodi danno risultati identici, il dimensionamento della linea di base è preferito anche se il progettista deve fare alcuni calcoli per esprimere tutte le dimensioni provenienti dall’origine del dato. Farlo una volta sola preclude (ngăn ngừa, làm cho không thể xảy ra) innumerevoli calcoli soggetti a errori lungo la strada.
I dati per il controllo posizionale: Ogni tolleranza posizionale deve fare riferimento a uno, due o tre datum. Il DRF non deve necessariamente limitare tutti i sei gradi di libertà, solo quelli necessari per stabilire un orientamento e una posizione unici per la vera posizione. Es: Il DRF stabilito nella figura di destra limita solo quattro gradi di libertà. I due gradi rimanenti, rotazione e traslazione lungo l’asse di riferimento, non hanno alcuna attinenza con la vera posizione dell’elemento controllato. Così, ulteriori riferimenti all’origine sono senza senso e confondono.
Per molte tolleranze di posizione, come quelle nella figura di destra, la vista del disegno rende abbastanza ovvio quali caratteristiche del pezzo sono le origini, anche se non sono state identificate come caratteristiche di origine e referenziate nella cornice di controllo della caratteristica. Anche se siamo d’accordo sul fatto che i bordi sinistro e inferiore della parte sono chiaramente caratteristiche di origine, potremmo non essere d’accordo sulla loro precedenza nello stabilire l’orientamento del DRF. In un altro esempio, dove una parte ha più diametri coassiali, potrebbe essere ovvio per il progettista, ma molto poco chiaro per il lettore, quale diametro dovrebbe essere la caratteristica di riferimento. Per queste ragioni, Y14.5 non ha più permesso le origini implicite.
La tolleranza di posizione è un controllo di dimensionamento e tolleranza geometrica (GD&T) usato sui disegni di ingegneria per specificare la posizione desiderata, così come la deviazione consentita alla posizione di una caratteristica su una parte.
- Una tolleranza di posizione definisce la deviazione consentita dalla posizione vera.
- La tolleranza per una posizione vera o una dimensione di base deve provenire da una tolleranza geometrica.
- Quando si usa una tolleranza di posizione, deve essere definita la posizione vera della caratteristica di dimensione.
Requisiti della tolleranza di posizione:
- Deve essere applicata a una caratteristica di dimensione o a un modello di caratteristiche di dimensione.
- Le dimensioni di base utilizzate per definire la posizione reale.
- Devono essere utilizzati riferimenti di data (tranne quando applicata a diametri coassiali).
- RFS è la condizione di default a meno che non sia specificato MMC o LMC.
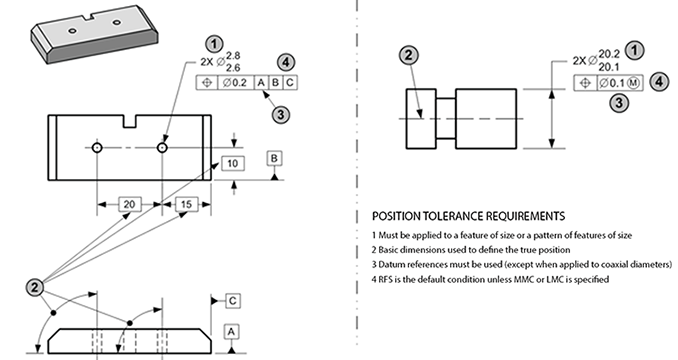
Le due forme di zona comuni per una tolleranza di posizione.
Modificatori che possono essere usati con una tolleranza di posizione, e quando ogni modificatore di condizione materiale (MMC, LMC, o RFS) dovrebbe essere usato in una tolleranza di posizione. Il modificatore M riduce il costo di produzione. Il modificatore P è usato per l’allineamento.
Due interpretazioni delle zone di tolleranza per le tolleranze di posizione. Posizione asse RFS e posizione superficie MMC.
- Quando dovrebbe essere usata l’interpretazione di superficie per una tolleranza geometrica? Quando il modificatore MMC è specificato nel quadro di controllo della caratteristica. Interpretazione della superficie per la tolleranza di posizione su un modello di fori. Interpretazione della superficie per la tolleranza di posizione su una larghezza.
Interpretazione dell’asse/piano centrale per la tolleranza di posizione su una serie di fori: L’asse dell’involucro di accoppiamento effettivo non correlato deve trovarsi all’interno della zona di tolleranza. I cilindri della zona di tolleranza sono situati e orientati in base alle dimensioni di base. La variazione di orientamento degli assi è limitata dal cilindro della zona di tolleranza. Schema di fori controllati con TOP usando RFS. Diametri coassiali controllati con TOP usando RFS.
Interpretazione del piano centrale per la tolleranza di posizione su una larghezza: il piano centrale dell’involucro di accoppiamento reale non correlato deve essere all’interno della zona di tolleranza. Il simulatore dell’origine consiste in due piani paralleli che contattano il pezzo per stabilire il piano centrale dell’origine.
Tolleranza di posizione e condizioni applicate a RFS:
- dove una tolleranza di posizione è applicata a RFS, una tolleranza bonus non è permessa.
- dove una tolleranza di posizione è applicata a RFS, viene usata l’interpretazione asse/piano centrale.
- dove una tolleranza di posizione è applicata a RFS, la zona di tolleranza è situata dalle dimensioni base.
Tolleranza di posizione e condizioni che si applicano a MMC:
- dove una tolleranza di posizione si applica a MMC, è permessa una tolleranza bonus.
- Qualora si applica una tolleranza di posizione a MMC, l’interpretazione asse/piano centrale non è usata.
- Qualora si applica una tolleranza di posizione a MMC, la zona di tolleranza è localizzata dalle dimensioni di base.
Tolleranza di posizione e caratteristiche angolari: La tolleranza di posizione è particolarmente adatta alle caratteristiche angolari per tutta la loro lunghezza. Questo presuppone (cho là, coi như là) che la feature non abbia un’interfaccia funzionale (mặt phân giới) oltre la sua lunghezza e larghezza (bề ngang, bề rộng, khổ). Tuttavia, nella figura di destra, un perno viene premuto nel foro controllato e ci si aspetta che si accoppi con un altro foro in una piastra di copertura. L’elemento di accoppiamento non è il foro del perno stesso, ma piuttosto il perno, che rappresenta una proiezione del foro. Allo stesso modo, l’interfaccia di accoppiamento non è all’interno della lunghezza del foro del perno, ma sopra il foro, nello spessore della piastra di copertura. Vedi Figura. Stabilire posizioni vere da un dato implicito – un errore comune.
Se il foro del perno fosse perfettamente perpendicolare all’interfaccia progettuale tra le due parti, non ci sarebbe differenza tra la posizione del foro e del perno. Qualsiasi angolazione (hình có góc), tuttavia, introduce una discrepanza (sự khác nhau) nella posizione. Questa discrepanza è proporzionale (tương ứng về cỡ, số lượng hoặc mức độ ; có tỷ lệ đúng; cân xứng) alla lunghezza della proiezione. Quindi (do đó, theo đó, vì thế, vì vậy), controllare direttamente la posizione del foro del perno stesso è inadeguato (không tương xứng, không xứng, không thích đáng, không thoả đáng) ad assicurare l’assemblabilità. Quindi (bởi vậy, cho nên, vì thế, vậy thì), la posizione della proiezione del foro (hình chiếu) doveva essere controllata, che potrebbe essere pensata come un perno fantasma. questo si realizza con una tolleranza posizionale modificata con una zona di tolleranza proiettata.
Tolleranza posizionale e zona di tolleranza proiettata. L’applicazione di questo concetto è raccomandata quando la variazione di perpendicolarità dei fori filettati o a pressione potrebbe causare l’interferenza di elementi di fissaggio, come viti, perni o spine, con le parti di accoppiamento. Nella figura 1.a, un’interferenza può verificarsi quando viene specificata una tolleranza per la posizione di un foro filettato o a pressione, e il foro è inclinato entro i limiti di posizione. A differenza dell’applicazione di un elemento di fissaggio flottante che coinvolge solo i fori liberi, l’atteggiamento di un elemento di fissaggio fisso è governato dall’inclinazione del foro prodotto in cui si monta. La figura 1.b illustra come il concetto di zona di tolleranza proiettata tratta realisticamente la condizione mostrata nella precedente figura 1.a. Si noti che è la variazione di perpendicolarità della porzione di elemento di fissaggio che passa attraverso la parte di accoppiamento ad essere significativa. La posizione e la perpendicolarità del foro filettato sono importanti solo nella misura in cui influenzano la porzione estesa dell’elemento di fissaggio che si impegna. Quando le considerazioni di progettazione richiedono un controllo più stretto della perpendicolarità di un foro filettato rispetto a quello consentito dalla tolleranza di posizione, può essere specificata una tolleranza di orientamento applicata come zona di tolleranza proiettata.
Una zona di tolleranza proiettata è definita per prevedere le dimensioni finali e le posizioni delle caratteristiche su un componente o un assemblaggio soggetto a tolleranza. Una zona di tolleranza proiettata esce al di fuori dell’estensione della caratteristica di tolleranza delle dimensioni. Una zona di tolleranza proiettata è specificata mettendo il simbolo P con un cerchio dopo il valore di tolleranza nel quadro di controllo della caratteristica di posizione. Questo stabilisce una zona di tolleranza centrale di dimensione costante (kích thước, cỡ, khổ không thay đổi) delimitata o da due piani paralleli separati da una distanza pari alla tolleranza specificata, o da un cilindro con un diametro pari alla tolleranza specificata. Per i fori ciechi e altre applicazioni in cui la direzione della proiezione è ovvia, la lunghezza della proiezione può essere specificata dopo il simbolo nella cornice di controllo della caratteristica. Questo significa che la zona di tolleranza proiettata termina alla faccia del pezzo e alla distanza specificata dalla faccia del pezzo (lontano dal pezzo e parallelo all’asse di posizione reale o al piano centrale). La lunghezza della proiezione dovrebbe essere uguale all’estensione massima dell’interfaccia di accoppiamento. In Figura. a (esempio di perno e piastra di copertura). la lunghezza della proiezione deve essere uguale allo spessore massimo della piastra di copertura .38. Se necessario, l’estensione e la direzione della zona di tolleranza proiettata sono mostrate in una vista del disegno come un valore quotato con una linea a catena pesante disegnata accanto alla linea centrale della caratteristica come in Figura. b.
- In RFS: L’asse esteso o il piano centrale dell’involucro di accoppiamento effettivo della caratteristica (come definito in Elementi derivati) deve essere contenuto all’interno della zona di tolleranza proiettata.
- In MMC: L’asse esteso o il piano centrale del limite di forma perfetta MMC di livello 2 applicabile alla caratteristica (come definito in Livello 2 – Forma complessiva della caratteristica) deve essere contenuto nella zona di tolleranza proiettata. Questo esempio spiega che man mano che le dimensioni dell’elemento si discostano dalla MMC, l’elemento si adatta al suo limite di forma perfetta MMC in modo più lasco. Questo permette una maggiore deviazione nell’orientamento e/o nella posizione dell’elemento. L’allontanamento di un foro dalla MMC permette l’assemblaggio con un perno di accoppiamento che ha il suo asse ovunque all’interno di una zona conica (hình nón). Il metodo alternativo del centro descritto in (Livello 2 – Forma complessiva della caratteristica) non può essere utilizzato per una zona di tolleranza proiettata. La sua tolleranza bonus semplicemente allargherebbe la zona di tolleranza proiettata uniformemente lungo la sua lunghezza proiettata, non riuscendo ad emulare il vero potenziale funzionale della caratteristica.
- In LMC: (pagina 5-120)…
Verifica una tolleranza di posizione con il modificatore di zona di tolleranza proiettata: Un metodo comune per verificare una zona di tolleranza proiettata è quello di usare un perno di calibro inserito nella caratteristica di tolleranza della dimensione con un’estensione che sporge in alto per l’altezza della zona di tolleranza proiettata. L’altezza di una zona di tolleranza proiettata è spesso determinata dall’altezza massima del foro nella parte corrispondente.
Tolleranza posizionale al MMC: Una tolleranza posizionale applicata al MMC può essere spiegata in termini di superficie o di asse della caratteristica di dimensione. In certi casi di deviazione estrema della forma (entro i limiti delle dimensioni) o di orientamento del foro, la tolleranza in termini di asse può non essere esattamente equivalente alla tolleranza in termini di superficie. Vedere Im_1-13. In questi casi, l’interpretazione della superficie ha la precedenza. In alcuni casi, la tolleranza aggiuntiva può indirettamente avvantaggiare caratteristiche diverse da quella che si è allontanata dalla MMC.
- Interpretazione della superficie: Pur mantenendo i limiti dimensionali specificati della caratteristica, nessun elemento della superficie deve violare un confine teorico (condizione virtuale) situato in posizione reale. Vedere Im_1-14.
- Quando dovrebbe essere usata l’interpretazione della superficie per la tolleranza geometrica? Quando il modificatore MMC è specificato nel quadro di controllo della caratteristica, vedere (Interpretazione della superficie per la posizione su un modello di fori – Interpretazione della superficie per la tolleranza della posizione su una larghezza – Interpretazione asse/piano centrale per la tolleranza della posizione su un modello di fori – Interpretazione del piano centrale per la tolleranza della posizione su una larghezza).
- Interpretazione asse o piano centrale: Quando una caratteristica di dimensione è a MMC, il suo asse o piano centrale deve cadere all’interno di una zona di tolleranza situata nella posizione vera. La dimensione di questa zona è uguale alla tolleranza di posizione. Vedi Im_1-15, (note/illustrazioni n. 1 e 2). Questa zona di tolleranza definisce anche i limiti di variazione dell’orientamento dell’asse o del piano centrale della caratteristica di dimensione rispetto alla superficie di riferimento. Vedi Im_1-15, (nota/illustrazione n. 3). La zona di tolleranza specificata si applica solo quando l’elemento di dimensione è a MMC. Dove la dimensione dell’involucro di accoppiamento effettivo non correlato dell’elemento di dimensione si discosta da MMC, risulta un’ulteriore tolleranza di posizione. Vedi Im_1-16. Questo aumento della tolleranza posizionale è uguale alla differenza tra il limite massimo delle condizioni del materiale specificato per la dimensione (MMC) e la dimensione effettiva non correlata dell’involucro di accoppiamento. Quando la dimensione effettiva non correlata dell’involucro di accoppiamento si è allontanata dal MMC, la tolleranza di posizione specificata per un elemento di dimensione può essere più grande del valore dichiarato e soddisfare ancora i requisiti di funzione e intercambiabilità.
Specificare la tolleranza di posizione al MMC: Quando il simbolo di condizione materiale massima (MMC) è specificato per modificare la tolleranza di un elemento di dimensione in un quadro di controllo della caratteristica, si applicano i seguenti due requisiti:
- La tolleranza specificata si applica alla dimensione MMC della caratteristica. La MMC di una feature di dimensione è l’albero più grande e il foro più piccolo. La dimensione MMC di un elemento non deve essere confusa con il modificatore MMC, cerchio M.
- Quando la dimensione effettiva dell’involucro di accoppiamento dell’elemento si allontana da MMC verso LMC, si ottiene una tolleranza bonus nella quantità esatta di tale allontanamento.